Workbench
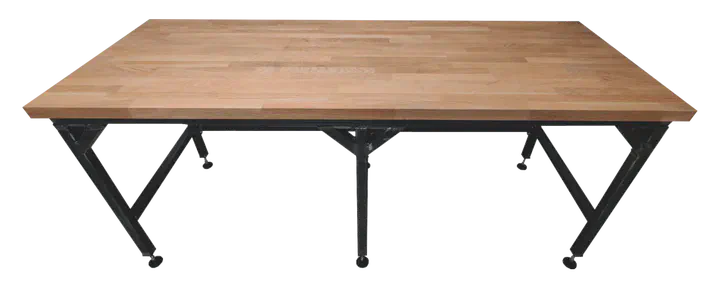
For every kind of work, there exists a table. Any kind of work can be performed on any kind of table, but the work is tremendously more fun when it’s on the right table.
For a workbench, the requirements are particularly high. The tabletop should be able to withstand the abuse of pounding and scratching and the underbody should stay firmly in place when doing so. Shearing the feet of the table is especially hindering when trying to work precisely because it leads to the work surface rocking from side to side. Stable construction and a heavy work surface are needed. Unfortunately, this makes it hard to move the bench, let alone get it into its predestined space if that space is somewhere in the basement. So the decision was made to go for a modular construction so that the individual pieces can be assembled on the spot.
Front view of the workbench Side view of the workbench
Design
The first step for any project is always a sketch in my notebook. Here the requirements and materials are specified, which outlines a general approach and provides a first design.
Modularity
The frame of the table can be separated into six individual parts, which are all light enough to be carried by a single person. They are hold together by M10 screws which mate with tapped, flat steel pieces that are welded to the tubes.
Tabletop
The most economic option would have been to use an off-the-shelf kitchen top from the hardware store. But here in Germany, these are only about 60 cm wide, which is not enough for my needs. So I settled on a solid 40 mm thick 2000 x 720 mm oak worktop, which I bought online. Over time the tabletop can expand and shrink orthogonal to the wood grain. When working with solid wood (e.g. not MDF or multiplex) it’s important to allow for this movement in the wood. Here this is done by seating the screws that hold onto the wood into slits that are cut into the steel frame. These slits have to be orthogonal to the wood grain.
Feet
To compensate for an uneven floor the legs feature adjustable feet for leveling. For this, a 10 mm thick plate is welded to the bottom of each foot. They are drilled and tapped with a M10 thread.
CAD
The entire cad-process from sketch to drawing was done in Autodesk Fusion360. The design you see below is my third iteration, I had to start over because the way I set up my sketches wasn’t allowing my to move forward efficiently.
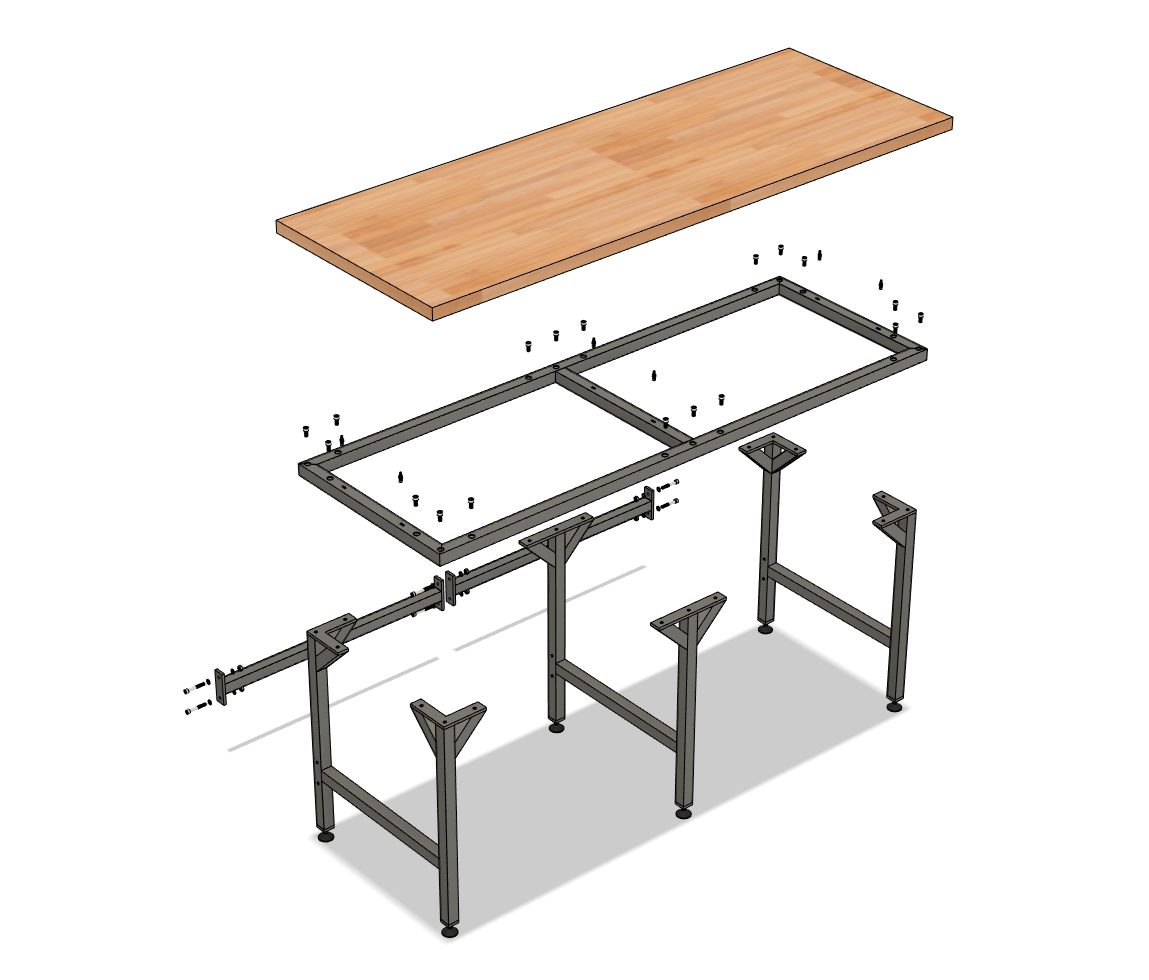
Explosion drawing
Editing the and adjusting the model is easy to do since the design is parametric, feel free to try it yourself.
To do so you will need to open the .f3z
archive file in Fusion360. Visit the change parameters pane to edit it’s dimensions. Please visit my GrabCAD page where I have uploaded the .step
and .f3z
files.
Drawings
Since I built this project in the summer of 2021, before I even had any plans to document my workings on an English website, I can unfortunately only provide German drawings. However, you may use these plans for free and do whatever you want with them. If you do decide to build it, I would appreciate it if you could reach out and let me know, thank you.
Fabrication
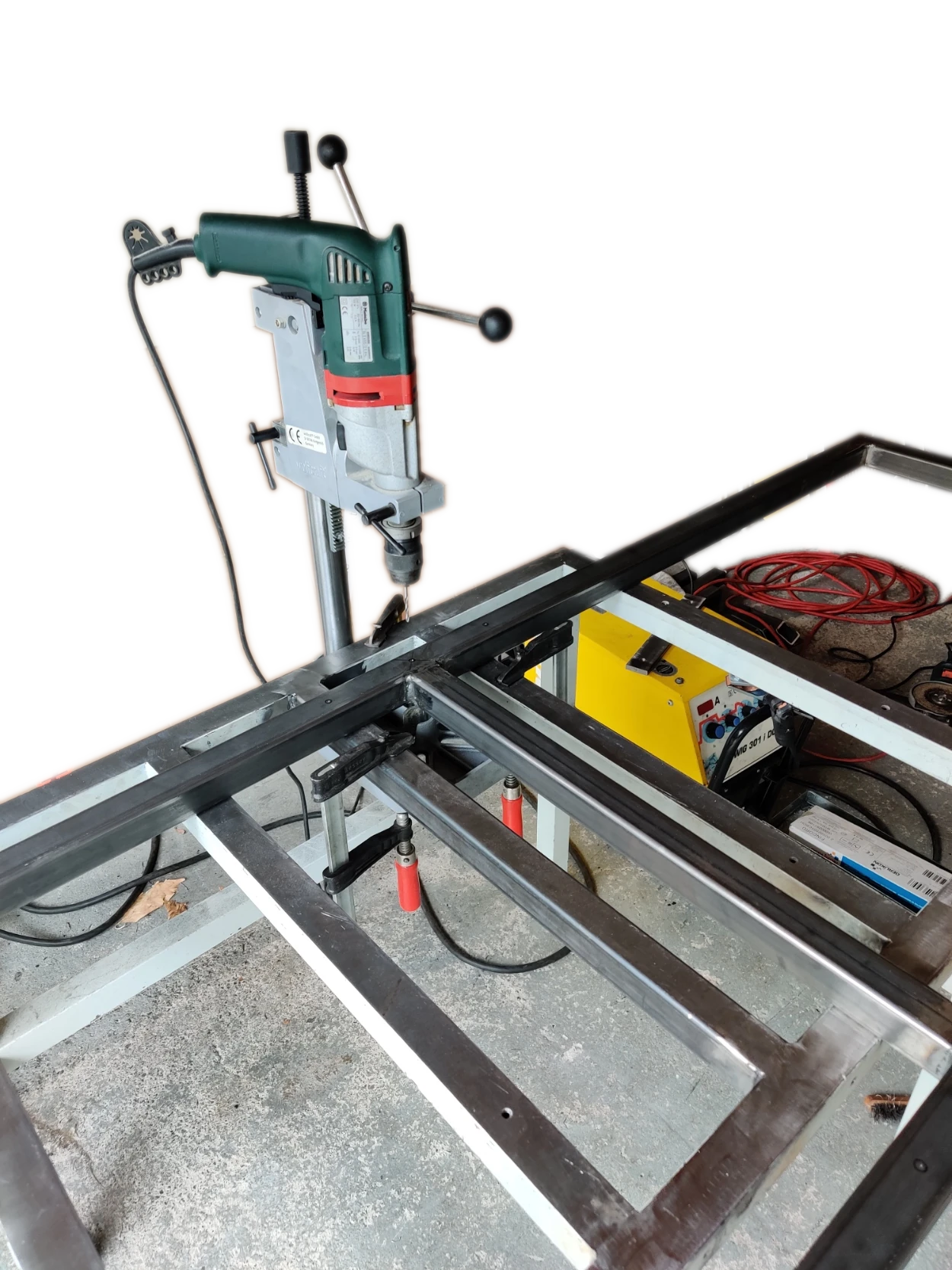
A drill stand clamped to an old table frame on which the workpiece lies.
The problem with building your first workbench is having no workbench to build the workbench on. So you might choose to sit on the ground and lean over the workpiece but if you want your finished table to be flat and not follow the form of your crooked concrete garage floor you will have to get a bit more clever. A possible solution would be to offset the workpiece from the ground in exactly three spots, thus defining a new plane. But with only three points of contact work holding becomes quite challenging without specialist equipment since you can’t just clamp it down to a known flat surface. Fortunately for me, I found a solid metal frame from an old laboratory table somebody wanted to throw away. So I repurposed that one as my fabrication table, figuring if the precision of the frame was good enough for that table, it should also be fine for me.
Cost breakdown
Item | Prize |
---|---|
steel | 212,00 € |
worktop | 249,00 € |
consumeables | ~20,00 € |
total | 481,00 € |
Conclusion
Considering this was my first welding project, the welds turned out better than I expected. However, it also took much more time than I expected, because given my limited amount of work-holding options and experience I constantly had to move the workpieces around and clamp them in an optimal position for me to weld. In the end, the whole project took the better part of the summer but resulted in a satisfactory worktable. The table is clearly missing drawers and the angled beams in the corner could be left out in the front to make room for some.